Know Your Options: A Guide to the Main Types of Backflow Preventers
- bill57931
- 2 hours ago
- 2 min read
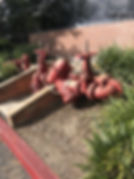
Protecting our drinking water from contamination is a critical aspect of public health and safety. One of the primary threats is backflow – the unwanted reversal of water flow that can pull pollutants or contaminants from sources like irrigation systems, boilers, or industrial processes back into the clean water supply.
To combat this, specialized devices called backflow preventers are installed. But not all backflow preventers are created equal; different situations require different types of protection.
Understanding the main types of backflow preventers helps ensure the right level of safety for your specific needs. Here’s a look at the most common ones:
Reduced Pressure Zone Assembly (RPZ)
What it is: Often considered the most reliable type, an RPZ consists of two independent check valves with a hydraulically operated, pressure-differential relief valve located between them.
How it works: If either check valve leaks, the relief valve opens to discharge water, maintaining a lower pressure zone between the valves than the supply pressure. This prevents backflow under both back-siphonage (low pressure in the supply line) and back-pressure (higher pressure downstream) conditions.
Common Uses: High-hazard applications where contaminants could pose a significant health risk (e.g., hospitals, chemical plants, irrigation systems using fertilizers/pesticides, boiler feeds).
Key Feature: Requires drainage as it's designed to discharge water. Must be tested annually.
Double Check Valve Assembly (DCVA)
What it is: As the name suggests, this assembly features two independent check valves operating in series.
How it works: Both check valves must fail for backflow to occur. It protects against back-siphonage and back-pressure but doesn't have a relief valve for visual indication of failure or discharge.
Common Uses: Low-to-medium hazard applications where contaminants are non-health hazards (e.g., food processing equipment where contaminants are non-toxic, fire sprinkler systems without chemical additives, large residential irrigation).
Key Feature: Does not discharge water under normal conditions. Must be tested annually.
Pressure Vacuum Breaker Assembly (PVB)
What it is: This device includes a single check valve and an air inlet valve.
How it works: It prevents back-siphonage by allowing air to enter the system if supply pressure drops, breaking the siphon. It does not protect against back-pressure.
Common Uses: Primarily used for irrigation systems (sprinklers) where the main hazard is back-siphonage and there are no downstream pumps creating back-pressure.
Key Feature: Must be installed at least 12 inches above the highest downstream outlet (sprinkler head or pipe). Testable.
Atmospheric Vacuum Breaker (AVB)
What it is: The simplest mechanical backflow preventer, consisting of a check valve and an air vent.
How it works: Similar to a PVB, it opens to admit air and break a siphon when pressure drops. It offers no back-pressure protection and cannot have any shut-off valves downstream.
Common Uses: Point-of-use protection like hose bibbs (outdoor faucets), utility sinks, or specific equipment connections.
Key Feature: Not testable in line. Inexpensive but limited application.
Choosing the Right Device
The appropriate backflow preventer depends heavily on the potential hazard level of the cross-connection and local plumbing codes. Always consult with a certified backflow prevention specialist or licensed Long Beach Plumber to assess your situation and ensure the correct type of device is installed and properly maintained for reliable water safety.